3D-printen, aanvankelijk een speeltuin voor hobbyisten om er hun dromen mee te realiseren, groeide de laatste jaren uit tot een volwaardige industriële productietechnologie. De hoeksteen van de additieve productie, waarbij laagje na laagje wordt toegevoegd om voorwerpen te maken, is 3D-metaalprinten. De belangstelling voor deze technologie neemt snel toe, ten nadele van de traditionele methodes om metalen onderdelen te vervaardigen voor engineering, productie en productieketens. De nieuwe technologie is snel: een product kan op één dag worden ontworpen, geproduceerd en getest. Ze is ook veelzijdig: het is mogelijk onderdelen met complexe vormen te maken zonder assembleren en boren en zelfs zonder ander gereedschap dan de printer. De technologie is bovendien nauwkeurig: kleine componenten - inclusief bewegende onderdelen - zijn uiterst gecontroleerd in één stuk te maken met extreem lage toleranties en dus met een hogere kwaliteit. Bovendien levert additieve productie tot 90% minder afval op dan de traditionele methodes!
Klinkt dit allemaal niet fantastisch? Waarom is prototyping dan tot nu toe vrijwel de enige toepassing? En waarom aarzelen de meeste bedrijven om de technologie in te voeren? Omdat er een keerzijde is aan de medaille van 3D-metaalprinten: bedrijven moeten er veel kapitaal in investeren, over gespecialiseerde medewerkers beschikken en dure grondstoffen gebruiken. Met de huidige technologieën kunnen de kosten oplopen tot $1000 per pond aan geproduceerde onderdelen. Dit beperkt aanzienlijk de mogelijke toepassingen en het marktpotentieel. Wie erin slaagt om van 3D-metaalprinten een industrieel leefbare productiewijze te maken, zit op rozen. Met de steun van imec.xpand doet Fabric8Labs nu mee aan deze race, met een nieuwe printtechniek die zij ECAM noemen, wat staat voor electrochemical additive manufacturing of elektrochemische additieve productie. Onderdelen die met deze techniek worden gemaakt, voldoen aan alle eisen die aan 3D-printing worden gesteld of overtreffen ze, terwijl de cost of ownership tien keer lager ligt. Mede-oprichters Jeff Herman, CEO, en David Pain, CTO, leggen uit hoe ECAM een revolutie in de wereld van additieve metaalproductie zal ontketenen.
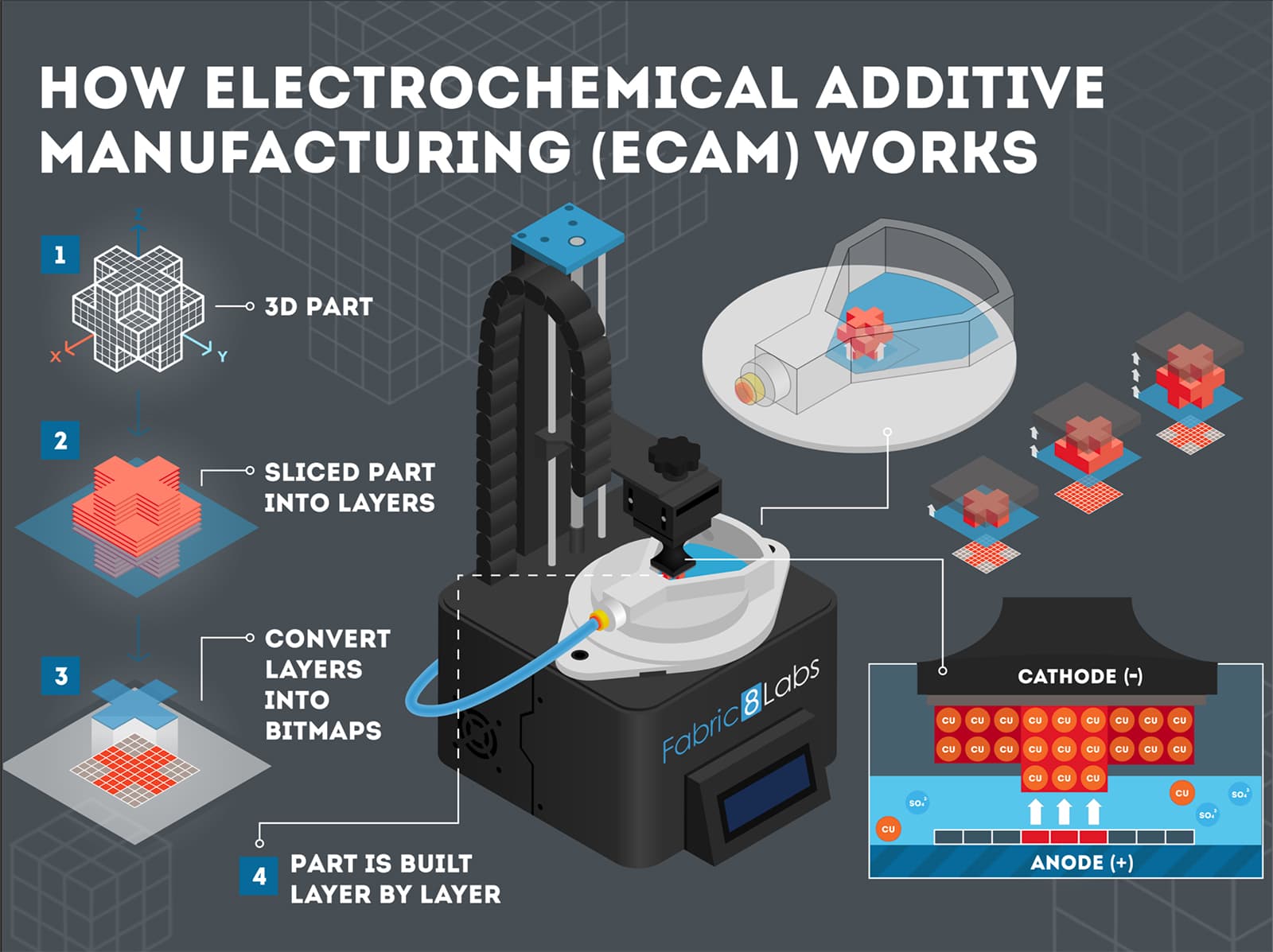
Het ECAM proces.
Een weldadig elektrochemisch bad
De oprichters van Fabric8Labs, die ervaring met industriële productie hebben, stelden vast dat de technologie voor 3D-metaalprinten te wensen overliet. De meeste geavanceerde processen steunen op een thermische techniek om metaalpoeders te versmelten. Maar de huidige machines met complexe lasersystemen en zelfs de metaalpoeders zijn heel duur. Dat beperkt momenteel de mogelijke toepassingen van 3D-metaalprinten. Fabric8Labs wil dit obstakel uit de weg ruimen met hun ECAM-printtechniek. Zij haalden hun inspiratie in de halfgeleidersector, die een gelijkaardige elektrochemische depositietechniek gebruikt om uiterst kleine structuren voor MEMS devices te maken. Fabric8Labs ontwikkelde ECAM tot een flexibele oplossing voor de 3D-printsector. De techniek laat thermische processen, lasers en poeders volledig links liggen en gaat voluit voor elektrochemische processen. Het materiaal waarvan zij vertrekken, bestaat uit een electrolytbad met opgeloste metaalzouten in. Als printkop gebruiken ze een micro-electrode array. Als de elektrodes in het gewenste patroon worden bekrachtigd, loopt er een stroom door het bad en wordt er materiaal afgezet.
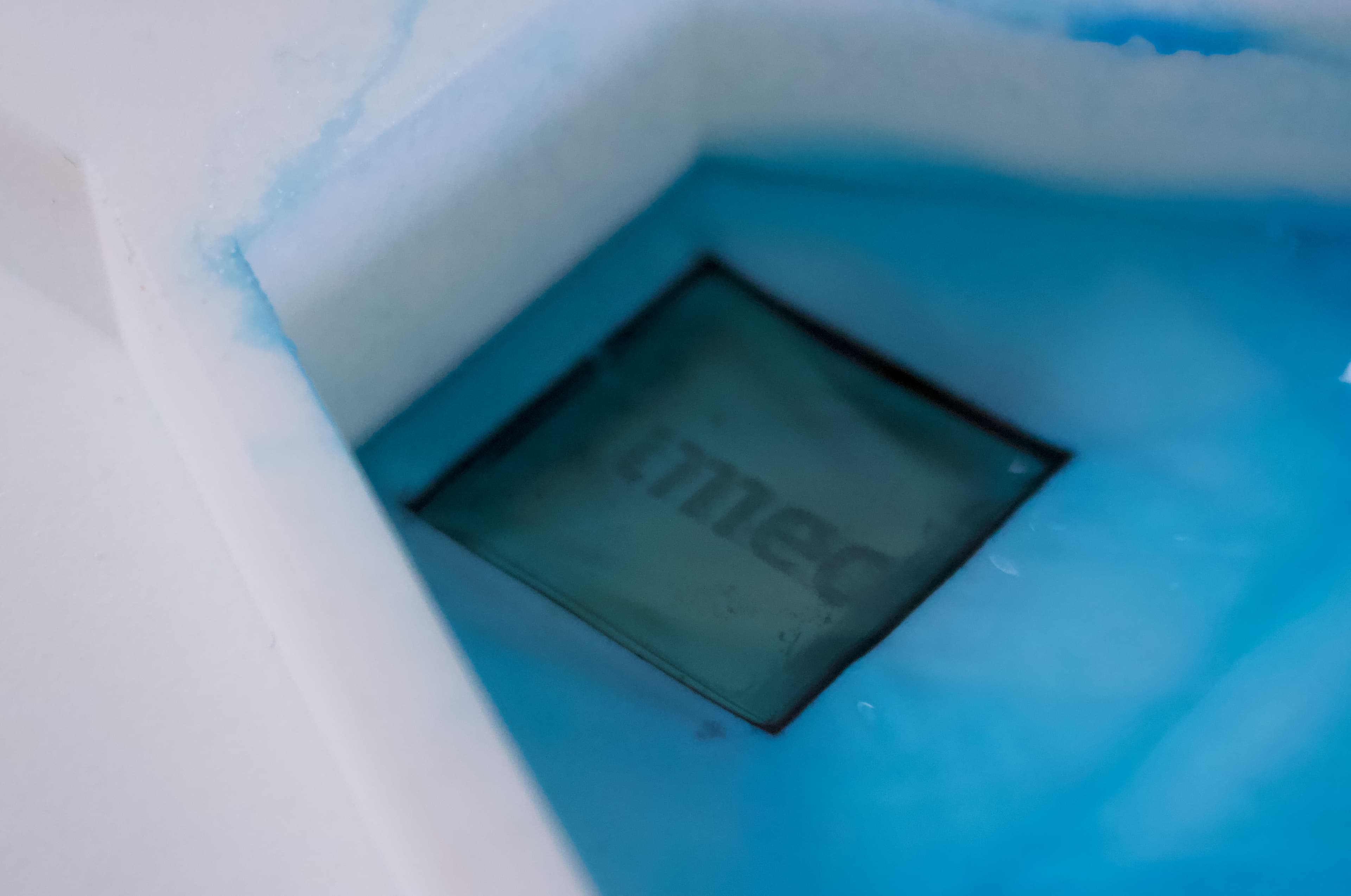
Geactiveerd anode array.
Hoe de elektrochemie lasers en poeders het nakijken geeft
Een van de grootste voordelen van deze techniek is het lagere prijskaartje. Daar zijn twee goede redenen voor. Om te beginnen is de printer zelf goedkoper, want hij functioneert zonder een van de duurste onderdelen van een traditionele 3D-metaalprinter: de laser. Ten tweede, en dit is nog belangrijker, is de elektrolyt in de ECAM-printer aanzienlijk voordeliger geprijsd dan de metaalpoeders. De verbruiksproducten zijn dus een orde van grootte goedkoper dan het huidige aanbod van concurrenten.
Maar dit is maar de helft van het verhaal. Wie erin slaagt om onderdelen op atoomschaal op te bouwen, boekt ook een kwaliteitsvoordeel. Bij het versmelten van metaalpoeders kunnen er microholtes ontstaan en kunnen er zich problemen met een ruwe afwerking en thermische spanningen voordoen. Het ECAM-proces heeft hier geen last van: het bouwt atoom per atoom op, zodat de objecten uiterst dens zijn en een zeer goede oppervlakte-afwerking.
In vergelijking met een lasersysteem biedt de techniek nog een ander voordeel: er wordt telkens een hele laag ineens opgebouwd in plaats van een laser die over het gehelen oppervlakte scant, waardoor opschalen eenvoudiger wordt. Daarom onderzoekt Fabic8Labs samen met imec de mogelijkheden om printkoppen voor steeds grotere toepassingen te ontwikkelen. Momenteel is de printkop en dus de te printen oppervlakte nog beperkt tot 1 vierkante inch (25 bij 25 mm), maar naarmate de technologie evolueert zullen printkoppen ter grootte van een flinke monitor of tv haalbaar worden. Daarmee produceer je dan kleine onderdelen in een lage tot gemiddelde oplage of zeer grote onderdelen. Bij lasersystemen is dit gewoonweg uitgesloten. Of je zou (dure) lasers moeten blijven toevoegen om op te schalen tot een groot bouwvolume. Terwijl bij ECAM gewoon geldt: hoe groter de printkop, hoe groter de oppervlakte die je in één keer opbouwt.
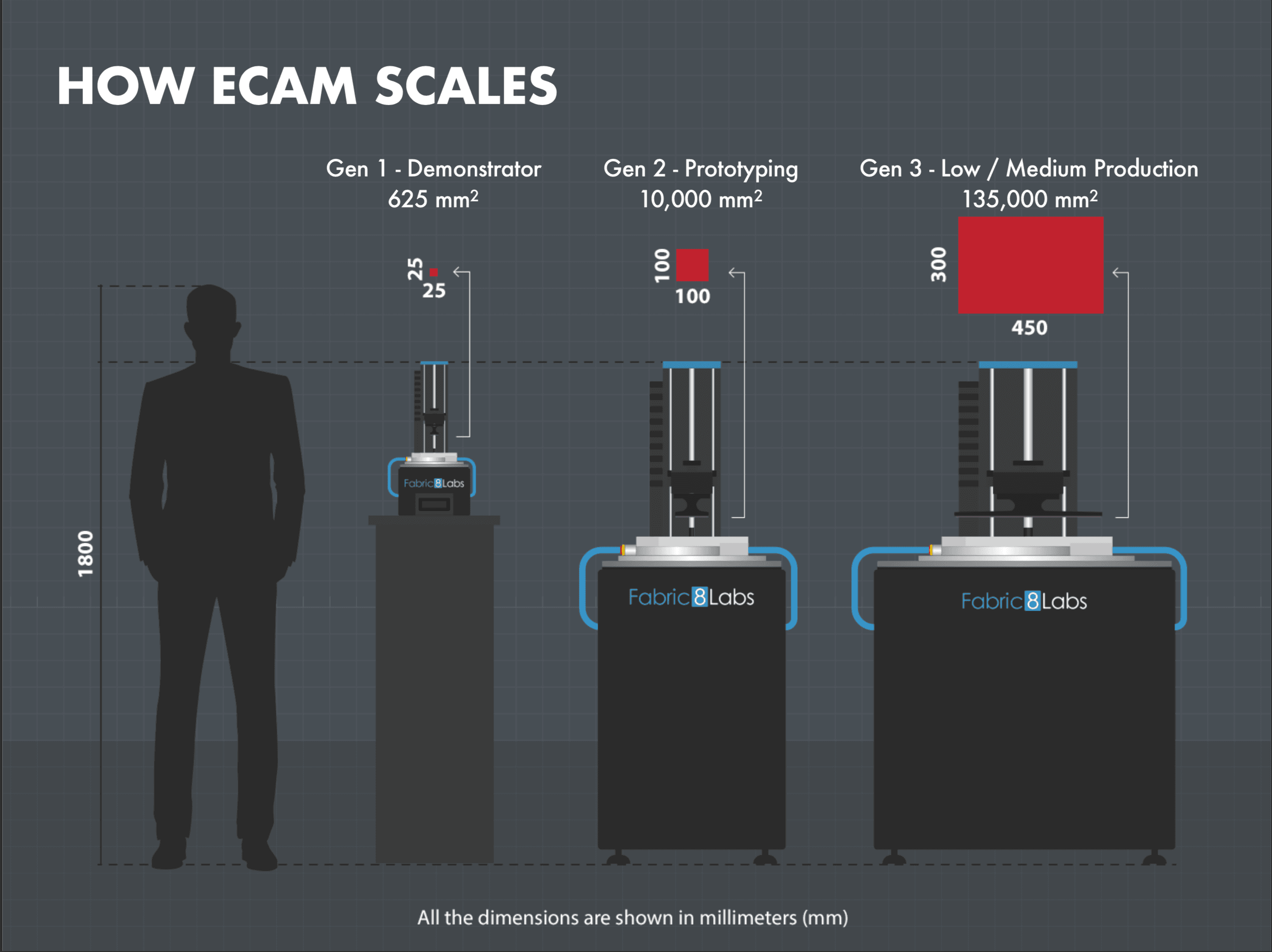
Het opschalen van de Ecam-printer.
Samenwerking met imec
De printkop is ook de reden waarom Fabric8Labs in een vroege fase met imec in zee is gegaan. Oorspronkelijk ging het om een grove, lageresolutie-toepassing van de technologie, met grote elektrodes. Het werd al snel duidelijk dat de halfgeleiderindustrie de logische partner is als het gaat om miniaturisatie. Om de micro-electrode array te ontwikkelen kwam de hulp van imec toen goed van pas, met hun ontwerpservices en expertise. De technologie werd geëvalueerd in een ontwerpstudie en gesimuleerd om ze geschikt te maken voor toepassingen. In het kader van deze samenwerking werd de printkop aangepast met dunne-film technologie zodat de eerste hoge-resolutie 3D-structuren konden geprint worden. Bovendien leidde imec.xpand de eerste investeringsronde van Fabric8Labs met de deelname van een Amerikaanse bedrijfsinvesteerder. imec.xpand is een onafhankelijk beheerd durfkapitaalfonds met toegevoegde waarde dat zich richt op hardwaregebaseerde nanotechnologie-innovaties waarbij imec-technologie, expertise, netwerk en infrastructuur een doorslaggevende rol in zullen spelen.
Imec zal ook in de toekomst bijstand verlenen met de unieke verwerking van de dunne-film-gebaseerde backplanes zodat deze chemisch resistent en dimensionaal stabiel worden, en met het ontwerp van de volgende generatie printkoppen. Momenteel is het kleine printvolume van 25 x 25 x 75 mm de grootste beperking. Klanten ontvangen momenteel dus slechts teststalen, zoals materiaalstalen, staafjes om de treksterkte van het materiaal te evalueren en kleine onderdelen. De printer van de volgende generatie, die volgend jaar wordt geïntroduceerd, zal onderdelen met een printoppervlakte van 100 bij 100 mm produceren. Nog later zullen printers van de derde generatie in staat zijn om onderdelen van zelfs 300 bij 450 mm te printen.
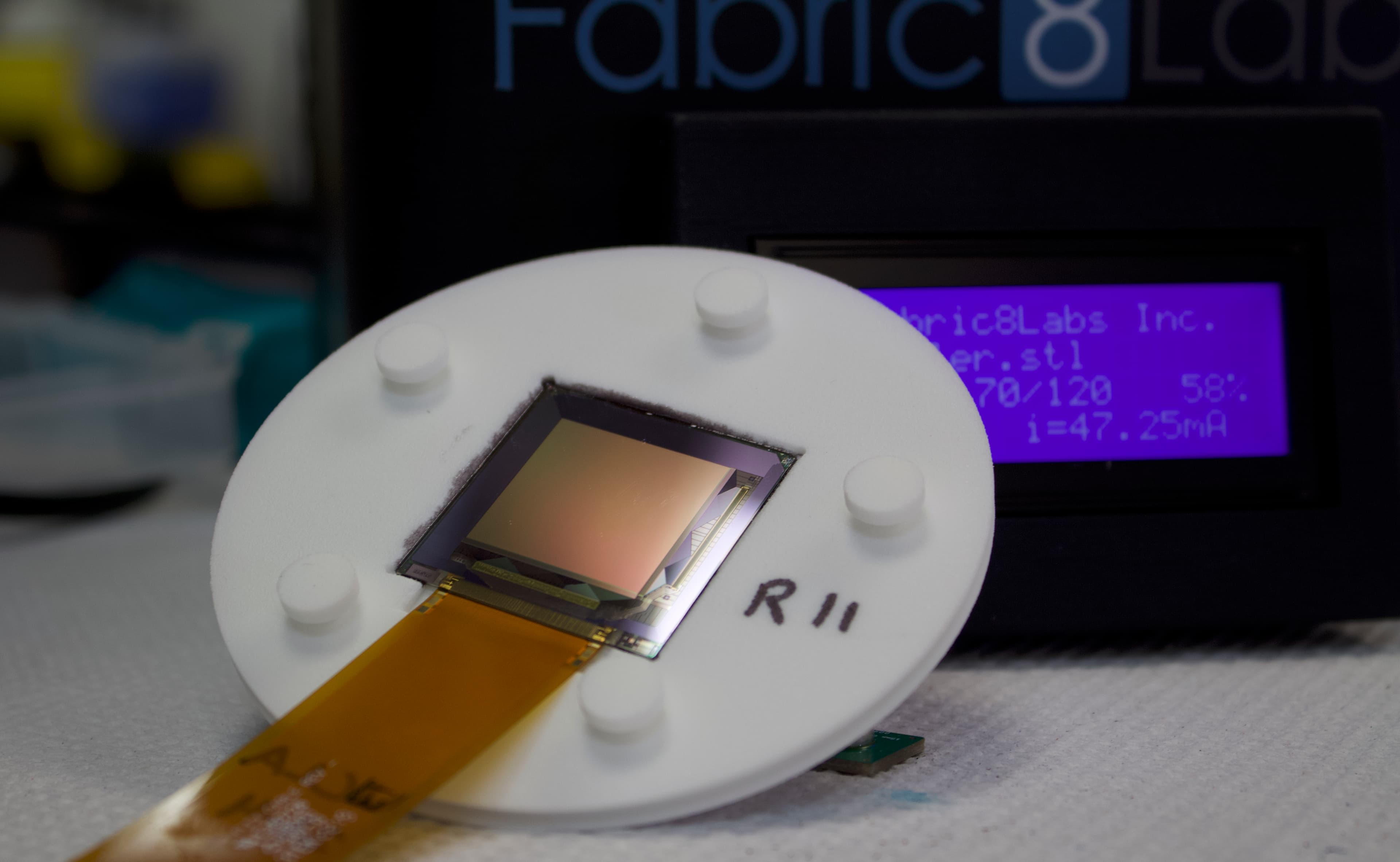
De printkop met dinne-film technologie.
Metalen en andere materialen
Qua resolutie of snelheid is de nieuwe 3D-printtechniek niet te verslaan, maar er kleven wel beperkingen aan de materialen. Voor de ECAM-techniek moeten de materialen immers in aanmerking komen voor elektroplating en zo zijn er momenteel maar 30 tot 40. Voor een aantal materialen is de techniek zeker niet geschikt, zoals complexe legeringen waarbij talrijke elementen onder controle moeten zijn. Toch is de lijst van voor ECAM geschikte materialen potentieel groot, aangezien het kan gebruik maen van alle vooruitgang in de electroplating industrie. Kopertoepassingen behoren alvast tot het laaghangende fruit, waarbij de ECAM-techniek echt het verschil maakt. Denk aan warmtewisselaars of chipverpakkingen voor halfgeleidertoepassingen waarbij sterk (elektrisch of thermisch) geleidend koper belangrijk is. Andere systemen hebben het moeilijk met koper, omdat het met een laser heel moeilijk te lassen is.
Onderdelen die uit meerdere materialen bestaan, vormen een ander dankbaar toepassingsdomein. Op lange termijn zullen niet alleen de binnen- en buitenkant van een object uit verschillende materialen kunnen bestaan, maar metalen en organische materialen zullen ook in één onderdeel kunnen worden gecombineerd. Eigenlijk kan alles wat voor elektroplating in aanmerking komt aan het proces worden aangepast. Zelfs met sommige kunststoffen lukt dit en met een aantal materialen die aan het bad kunnen worden toegevoegd om samen met het metaal te worden afgezet. Denk aan koolstofnanotubes of diamantpoeders, die nuttig kunnen zijn met hun unieke eigenschappen.
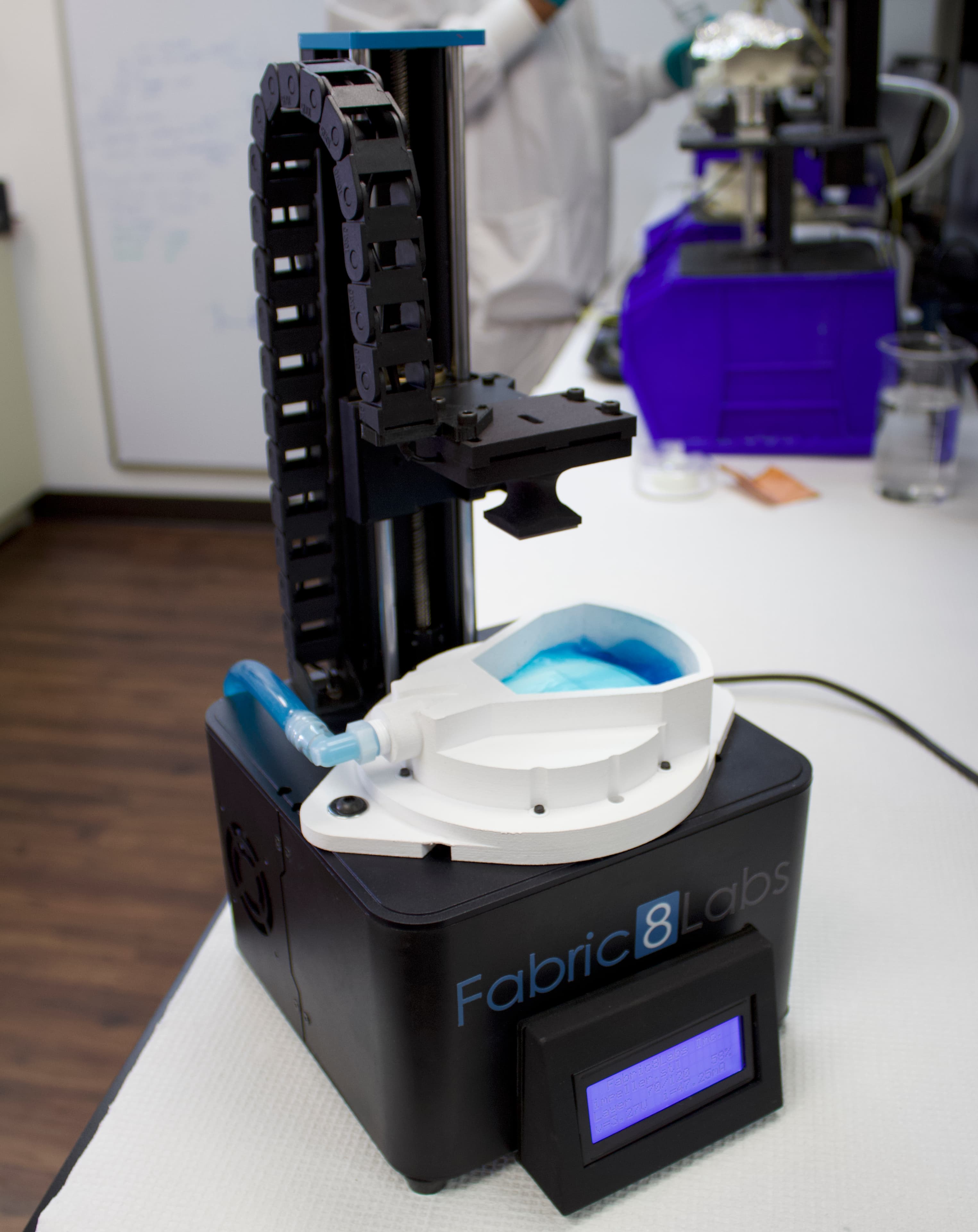
Gen-1 printer.
De toekomst van 3D-metaalprinten
Hoe zal deze techniek verder evolueren? Voor Fabric8Labs ligt de focus nu vooral op het opschalen van de printkoppen. Verder staat ook de ontwikkeling van andere materialen op de agenda, zoals verschillende nikkellegeringen. Hun chemieafdeling is al druk bezig met het ontwikkelen van de chemische baden. Multimateriaalprinten staat voor later gepland. Als we 5 tot 10 jaar vooruitkijken, zien we mogelijkheden om de pixels veel kleiner te maken voor het printen van MEMs structuren en metergrote printkoppen voor massaproductie . Dat betekent dus overstappen van de huidige mm-technologie naar printen op nanoschaal.
Fabric8Labs: “Als we erin slagen om de pixels te schalen van micrometer- naar nanometerschaal, dan staan er ons veelbelovende nanoschaal-toepassingen van deze technologie in de cleanroom te wachten.”
Meer weten?
- Lees meer over imec.xpand.
- Wil je meer weten over Fabric8Labs.
Gepubliceerd op:
30 augustus 2019